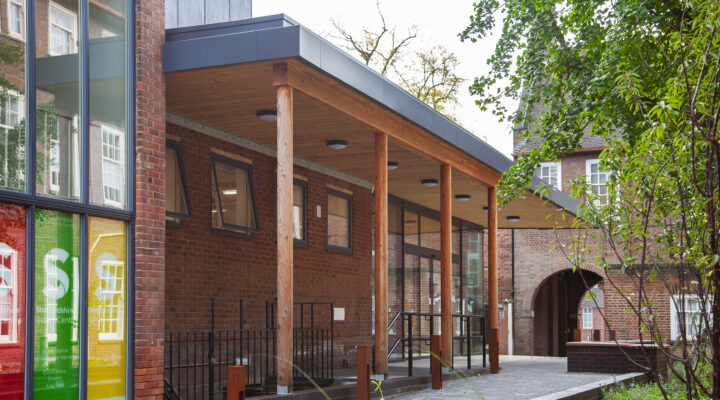
Multimillion Pound Burton Factory on Track
Pioneering roof tile manufacturer Russell Roof Tiles’ largest ever investment remains on track at its Nicolson Way site in Burton, with the final stage of construction and fit out now underway.
Work started on the £18.5m project last year which will double manufacturing output at the 9-acre site. The project is being commissioned in the autumn with full manufacturing to follow, the current plant continues to produce concrete roof tiles whilst the major scheme takes place.
The company makes concrete roof tiles and accessories for homes and building across the UK at two sites in Burton and one in Scotland and employs a team of 160.
Russell Roof Tiles is installing state-of-the-art manufacturing processes which support the firm’s Net Zero ambitions. This immense investment project has already seen the construction of a new groundbreaking batching plant, complete with mixer to facilitate increased concrete roof tile production. A high-tech curing chamber is also being fitted out and the final piece of the jigsaw will see the new factory extension under construction.
The new plant will increase efficiencies as well as sustainable benefits such as a water reclamation and refiltering system, that allows for recycling of all wash water, including using wash water from the factory. This will reduce the firm’s use of fresh water, and significantly reduce waste.
Across the whole project Russell Roof Tiles has been actively seeking ways to reduce its environmental impact, including investing in more energy-efficient equipment, optimising its production processes, and sourcing more sustainable materials as part of its Net Zero pledge, to ensure the company becomes carbon neutral by 2040, 10 years ahead of the Government’s timeline.
The project will deliver more manufacturing lines and a new 1600 sq/m building using a 30-ton steel frame which houses a state-of-the-art curing chamber for the concrete tiles, which is a significant part of the new plant.
Curing is an essential part of the successful manufacture of concrete roof tiles. The process takes place in a curing chamber at a temperature of around 37 degrees celsius and moisture is also added to the air to optimise the curing environment.
The more aesthetically demanding the concrete, the greater the importance of consistency of curing. For example, hot and cold spots in the chamber can impact the strength, and variations in temperature could lead to colour differences and reduced quality.
A team from Germany are currently installing the chamber, which houses floor to ceiling racking providing a carefully controlled gentle air flow (at 32 degrees celsius) across the tiles. The highly insulated chamber is very energy efficient. This system generates a constant air temperature and humidity within the chamber, and a consistent and optimum curing climate in a single atmosphere creates a microclimate. Not only will the new facility produce a product which is of higher quality, strength and consistency but it will also speed up the drying process.
Managing Director of Russell Roof Tiles, Andrew Hayward, comments “With the work having started on the factory extension we’re at a crucial stage in the investment and we have a huge number of different teams on site all working hard to ensure the project continues on track.”